杨紫娟1,3,田雪沁2,吴伟丽1,袁铁江3
(1.西安科技大学电气与控制工程学院,陕西省西安市710054;2.国网经济研究院有限公司,北京市102209;3.大连理工大学电气工程学院,辽宁省大连市116024)
摘要:纯氢运输成本高是阻碍电制氢消纳可再生能源技术发展的因素之一。采用混氢天然气(HCNG)技术,将氢气直接掺入天然气管道运输,能有效降低运输成本。针对管道掺氢时掺氢比控制问题和制氢设备容量配置问题,建立了风电-氢能-HCNG耦合网络。在分析电解槽单体过载效率特性基础上,对多电解槽模块化集成的电制氢系统运行特性进行分析,进一步提出多电解槽双层轮值协调运行策略。以系统收益最大为目标,考虑系统中功率、氢气平衡及各设备运行约束,建立了能够满足掺氢需求的氢能系统容量配置模型,并采用MATLAB调用CPLEX进行求解。通过算例分析和比较验证了管道掺氢在长距离输氢中的经济性及可行性,基于电解槽运行特性的双层轮值策略能够均衡电解槽运行时长、降低容量配置需求、减小投资成本。
0引言
在中国“碳达峰·碳中和”战略指导下,风电、光伏等可再生能源将逐步替代传统化石能源,占据能源领域主导地位。针对新能源消纳问题,大规模风光制氢已成为当前研究热点[1]。然而,安全、高效的氢气运输技术是氢能规模化应用的主要瓶颈之一。管道运氢运量大、成本低,但建设专用氢气管道需要时间和资金成本,利用混氢天然气(hydrogen enriched compressed natural gas,HCNG)技术将氢气直接掺入天然气管道,通过现有的天然气管网输送,可有效解决中国氢能基础设施建设不足的问题[2-3]。在风电制氢储能系统中采用HCNG技术,需要考虑掺氢比约束和电制氢设备特性,选取合适的容量和功率,优化系统配置,保证系统经济、稳定运行。
目前,国内外大量研究都证实了天然气管道掺氢的可行性。文献[4-5]通过对全球天然气掺氢研究现状、典型项目案例、技术问题与应用优势等方面的探讨,认为向已有的天然气管道设施中掺氢,是氢能发展前期降低氢气运输成本的有效解决方案之一。一方面,HCNG可以作为燃料直接供给家用燃气设备使用,但由于氢气与天然气的燃烧性质不同,不同掺氢比下HCNG的各项指标均不同。文献[6]通过计算华白数和燃烧势,证明掺氢比小于23%时能够满足燃气设备的正常使用。另一方面,HCNG通过天然气管道运输在终端进行分离后,氢气可以供给交通、化工领域。文献[7-8]表明,不同材质和压力的天然气管道允许的最大掺氢比也不同,文献[9]通过建立管道模型,证明氢气混入会增大管道出口压力。因此,在研究HCNG系统时,为减小对燃气设备及管道的影响,利用电制氢设备对掺氢量及掺氢比的控制至关重要。
电制氢技术的关键设备是电解槽。目前,碱性电解槽已经充分产业化,是大规模生产绿氢的最佳选择。文献[10]针对风电制氢导致电解槽间歇式运行的问题,提出了考虑制氢效率特性的风氢系统容量配置优化方法,通过研究电解槽的制氢效率特性,评估电解槽的最优工作区间。文献[11]针对电解槽功率调节特性,提出了阵列轮值优化策略,有效提升了电解槽阵列的寿命,但仅在风电出力大于电解槽容量时才会让部分电解槽过载,当风电出力小于电解槽容量时仍有部分时间单个电解槽的功率低于安全运行功率。文献[12]采用阶段式启停策略,电解槽效率和寿命都得到了显著提升,但当剩余功率低于所设置最低启动功率时会造成一定的弃风。文献[13]提出碱性电解槽宽功率适应模型,在降低系统运行成本的同时能够提高风、光资源利用率。文献[14]建立了海上风电-氢能系统配置优化模型,讨论了各种敏感因素对容量配置和经济性的影响,结果表明氢气价格和电解槽价格对系统的配置和收益影响最大。当前,对多电解槽组合协调运行的研究较少,在氢能系统中大多将电解槽看作一个整体,不考虑电解槽间的组合运行。
综上所述,本文在现有风电制氢储能系统的基础上结合HCNG技术,将氢气直接掺入天然气管道输送。基于电解槽单体工作特性,分析了多电解槽组合运行特性,提出了多电解槽双层轮值协调运行策略,并建立了考虑掺氢比约束的风电制氢储能系统容量优化模型。通过设置不同方案和场景对优化结果进行对比分析,验证了本文所提多电解槽运行控制模型在掺氢系统中应用的合理性及经济性。
1风电-氢能-HCNG耦合网络运行建模
1.1系统结构
HCNG的燃烧特性会随着掺氢比的变化而变化。为了不影响终端用户中燃气设备的使用,应使掺氢比尽可能保持恒定,即各时刻掺氢速率与天然气速率波动一致。然而,随机性风电出力难以保证制氢设备输出的氢气流始终满足掺氢需求。为此,需配置储氢罐,在弃风量富裕时将掺氢后的氢气存储,以保证弃风量为零时能够继续向HCNG系统提供恒定的氢气流。同时,考虑到风电出力不能满足电负荷的情形,需利用氢储能,通过燃料电池将氢气转化为电能供给负荷。
基于此,构建风电-氢能-HCNG耦合网络结构如图1所示,包含风电机组、天然气厂、电解槽、储氢罐、燃料电池、HCNG以及电负荷、燃气负荷。图中:vgas、vHCNG分别表示天然气速率和HCNG速率。
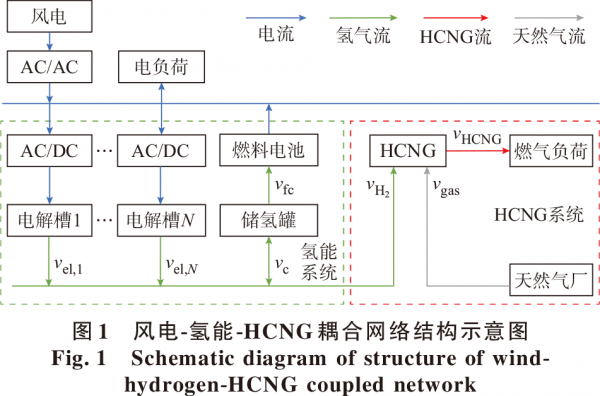
系统主要目的是在满足电负荷的前提下,利用氢能系统消纳弃风制氢,满足HCNG系统燃气负荷的掺氢需求,降低氢能运输成本。其中,制氢系统由多台电解槽并联运行,产氢速率为各台电解槽输出氢气量之和,即式(1);HCNG系统中氢气由氢能系统输入,电解槽和储氢罐输出氢气速率需始终满足管道掺氢和燃料电池用氢需求,即式(2)。
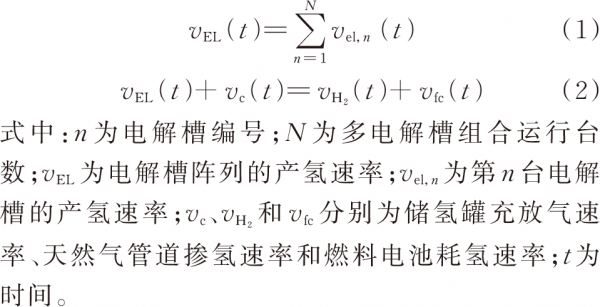
1.2 HCNG掺氢比
将氢气掺入天然气管道中输送,首先需要确定合适的掺氢比。掺氢比φ定义为氢气占HCNG的体积分数[4],而HCNG速率为天然气速率和氢气速率之和,故掺氢比和t时刻天然气速率决定了该时刻的掺氢速率。同时,根据国内学者研究,HCNG中掺氢比小于23%时能够不影响燃气设备的正常工作,且在低压天然气管道中掺氢比低于20%时不会产生氢脆现象[15-16],故将掺氢比限制在0~20%。掺混过程忽略了能量损耗和温度变化,如式(3)—式(6)所示。
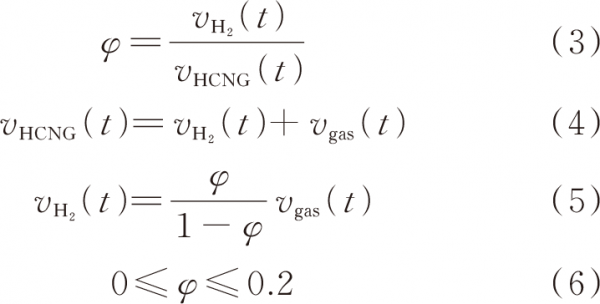
1.3储氢罐模型
储氢罐作为耦合网络中的氢气存储设备,其t时刻等效荷电状态(state of charge,SOC)由t-1时刻的SOC状态和储氢罐充放气量决定,如式(7)—式(9)所示。
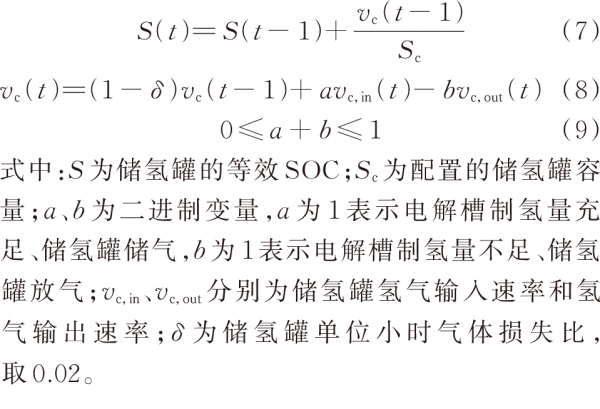
1.4燃料电池模型
由于质子交换膜氢燃料电池效率高且发展较为成熟,本文选用质子交换膜燃料电池。模型如下:
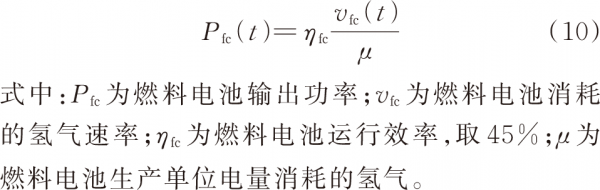
2碱性电解槽制氢单元运行模型
2.1电解槽单体运行特性
碱性电解槽具有如下特性:
1)高功率运行工况。电解槽在工作时,其功率可以短时超过额定功率,达到额定功率的110%~130%,但高功率运行会使电解槽产生热损耗,导致其运行效率降低[17]。α为其过载系数,取1.2。
2)低功率运行工况。电解槽的运行功率不能低于电解槽额定功率的20%,否则存在氢氧互串发生爆炸的危险[18],故电解槽最小安全运行功率为20%Pr,其中,Pr为电解槽额定功率。
3)电解槽的运行效率与输入功率有关,其运行效率达到最高点之后会随着输入功率的增大而缓慢降低[10],如附录A图A1所示。
电解槽产氢速率可表示为式(11)。根据运行效率与输入功率间的非线性关系,将产氢速率分段线性化,见附录A式(A1)。

4)碱性电解槽重新启动时需要耗费较长时间。这是因为电解槽开始启动时的温度无法满足氢气的生产条件,此时电解槽的功率都用来产生热量以提高温度[19]。
5)根据电解槽输入功率的大小将其运行状态分为4类,如式(12)所示。
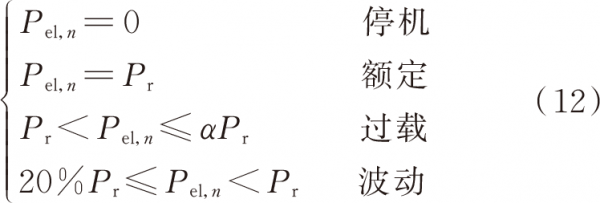
2.2多电解槽组合运行特性分析
由于单个电解槽容量较小,大型水电解制氢系统均由多个电解槽组合运行,组成的电解槽阵列具有如下特性:
1)拓宽系统运行范围。电解槽阵列的最低安全运行功率取决于单台电解槽的最低安全运行功率。单台电解槽容量越小,制氢单元可运行的范围就越宽,但电解槽容量越小,其单位投资成本越高。如附录A图A2所示,多台电解槽组合运行能够将系统运行范围从20%PR~αPR拓宽至20%Pr~αNPr。其中:

2)电解槽阵列整体效率特性。由单台电解槽的效率特性曲线可知,若使每台电解槽都始终工作在效率最高点,则电解槽负载率小,故需配置多台电解槽,造成投资成本过高;而配置台数过少,又会使电解槽长期运行在过载状态,导致电解槽整体效率降低、寿命缩短。因此,利用过载特性对系统进行配置时,需要充分考虑电解槽制氢效率特性曲线。
2.3多电解槽组合协调运行策略
基于上述对电解槽工作特性的分析,设计多电解槽组合协调运行策略,旨在满足HCNG掺氢速率的条件下,延长电解槽使用寿命,减少电解槽配置成本,保障电解槽安全运行。多电解槽协调运行策略分为两部分:首先,分析电解槽运行状态,确定t时刻额定、过载、波动、停机的电解槽数量及功率大小;其次,通过双层轮值策略确定电解槽运行的编号。
1)电解槽运行状态的确定。当有N台电解槽组合运行时,根据电解槽阵列的输入功率PEL,定义L为理论上应处于额定运行的电解槽台数,Pb为过载功率。L、Pb的计算公式如下:
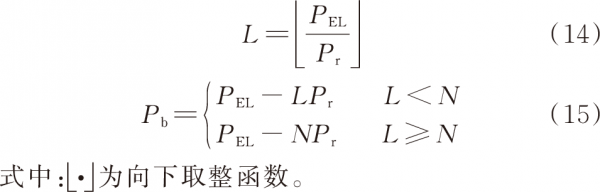
根据L的大小可分为以下两种情景:
情景1(L<N):若Pb<20%Pr,即过载功率无法满足下一台电解槽安全运行,则将已启动的电解槽置于高功率运行工况,从而避免电解槽处于低功率运行导致危险事故的发生;若Pb≥20%Pr,即剩余功率能够满足下一台电解槽安全运行,则启动下一台电解槽。Pb<20%Pr和Pb≥20%Pr时的电解槽运行状态分别如式(16)和式(17)所示。

2)电解槽运行编号的确定。采用双层轮值策略,即将电解槽的轮值策略分为两层。外层采用先启动先关闭的原则,使每个电解槽运行时长尽可能均衡。假设t时刻有n台电解槽运行,当输入功率增大时先启动编号较大的电解槽,当输入功率减小时先关闭编号较小的电解槽,以此类推。同时,考虑到电解槽过载时间不能过长,内层采用轮值策略,将过载及波动状态的电解槽在处于运行状态的电解槽中按照编号由小到大进行轮值,尽可能保证t时刻处于过载及波动状态的电解槽在下一时刻额定运行。电解槽双层轮值策略如附录A图A3所示。
3)轮值策略下电解槽过载时长限制。利用电解槽过载特性能够减少电解槽的配置容量,但当弃风量极大时,所有电解槽都将处于过载状态而无法进行内层的轮值。若为了降低配置成本,使电解槽始终运行在过载状态,将会极大地缩短电解槽运行寿命,这样反而增加了更换设备的成本。因此,在对电解槽容量进行配置时,还需考虑电解槽过载时长的限制。定义单台电解槽的过载率为过载时长占总运行时长的百分比,且过载率需小于等于0.5,如式(21)所示。
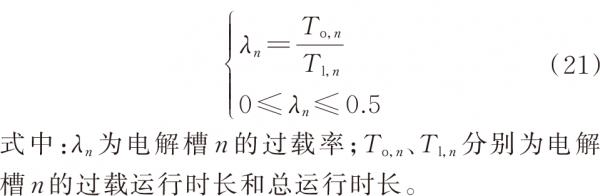
4)由于碱性电解槽首次启动需要耗费较长的时间,为避免电解槽频繁启停,根据电解槽运行状态部分的计算,当前电解槽运行台数与下一时刻运行台数之差大于等于1时才进行外层轮值,否则只进行内层轮值。此外,考虑到优化时间尺度大于电解槽启动时间,使用产氢速率惩罚来表示在启动时间中的能量损失[19]。电解槽产氢速率(式(11))改进为:
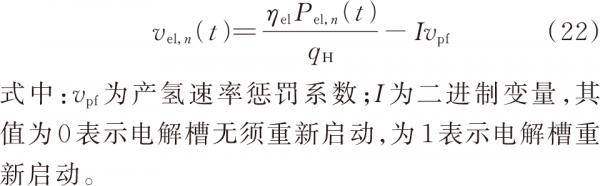
3氢能系统容量优化配置模型
基于2.3节多电解槽组合运行控制策略确定每台电解槽的运行功率,从而确定系统产氢量,进而影响系统容量配置及掺氢比大小,建立如下氢能系统容量优化配置模型。
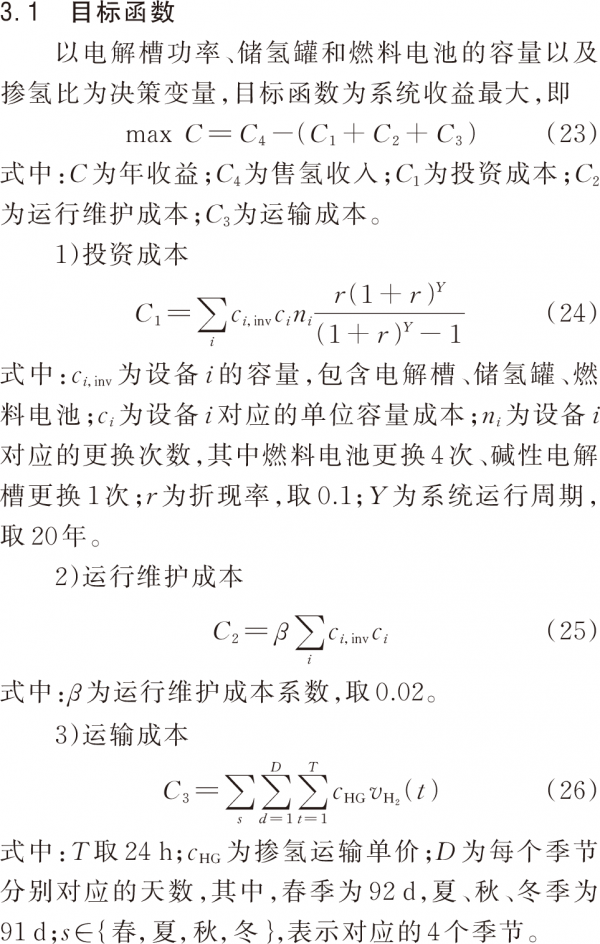
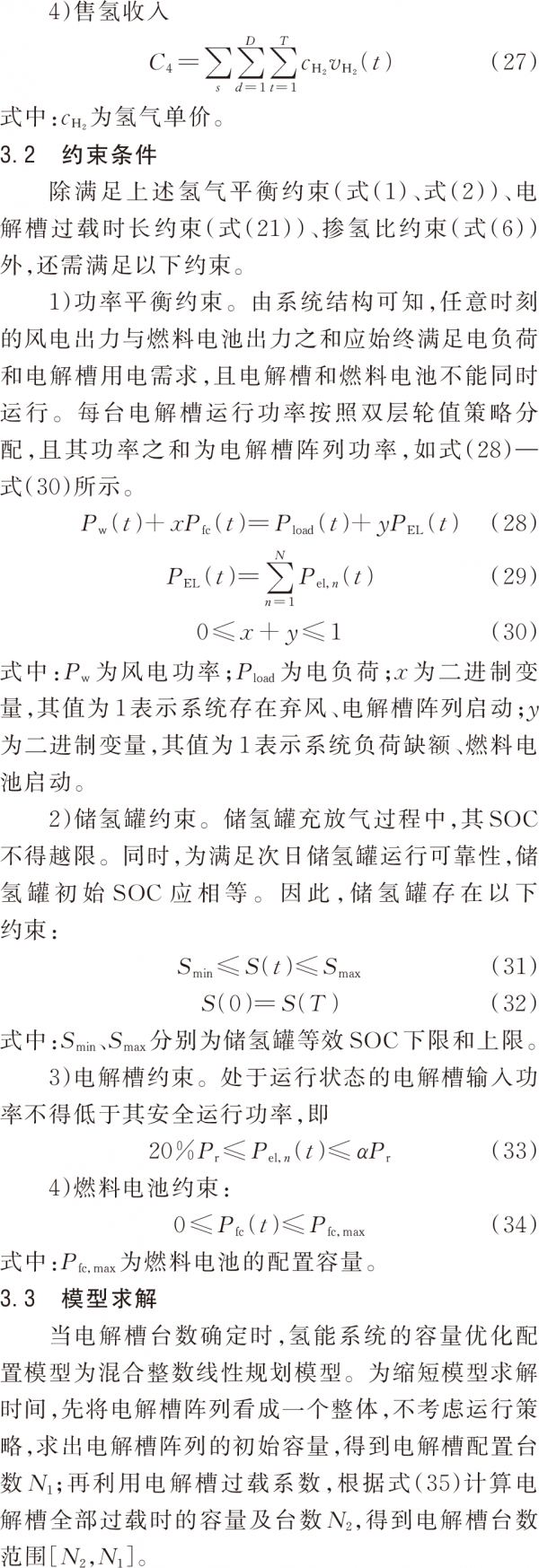
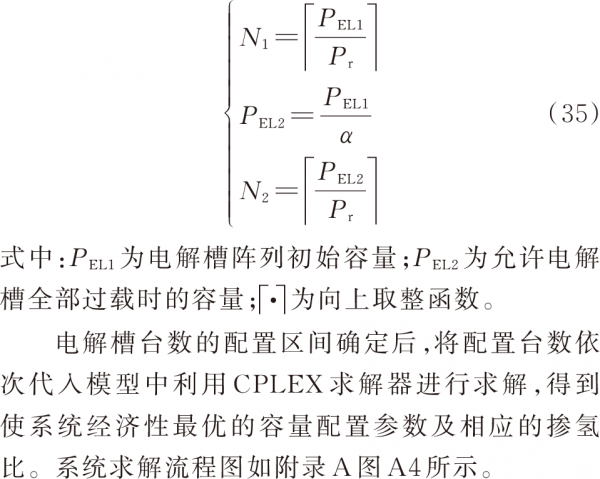
4算例分析
4.1算例介绍
根据上文建立的氢能系统容量优化配置模型,选取某地区春、夏、秋、冬不同季节的风、电、气负荷共12个典型日,如附录A图A5、图A6所示[20-21],图中管道长度为300km。其他设备参数如附录A表A1所示[22]。设置以下3种方案进行对比分析:
方案1:不设置HCNG系统,仅用氢能系统进行储能,以补偿风电不足时的电负荷,剩余氢气采用气瓶车进行运输,运输距离为300km。
方案2:采用本文网络结构,按照文献[11]中的缓慢启停策略进行容量配置,电解槽不运行在过载状态,设置启动功率为20%Pr。
方案3:采用本文网络结构,按照双层轮值策略进行容量配置。
4.2容量配置结果分析
1)不同方案容量配置结果分析
不同方案的系统容量最优配置结果见表1,系统各类费用见表2。结合表1、表2可知,由于气瓶车运输成本远高于管道掺氢运输,使得方案1的运行成本比方案2高1791.06万元,比方案3高1817.93万元。然而,方案1将制得的氢气直接通过气瓶车运输,除需储能以补偿风电低谷外无须大量存储,储氢罐配置容量分别约为方案2和方案3的1/4和1/3,故投资维护成本最低,总收益比方案2高204.97万元。方案2采用缓慢启停策略,电解槽不运行在过载状态,虽然电解槽制氢能力高,售氢收入大于方案3,但电解槽配置台数多导致投资维护成本增加,总收益减少,出现亏本。综上所述,采用轮值策略及掺氢运输的方案3收益最高。
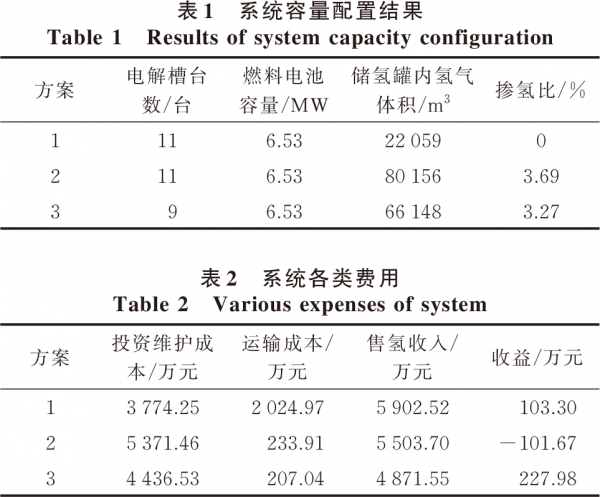
方案3在方案2的基础上,利用电解槽过载特性配置系统容量。根据式(35)得到电解槽台数配置区间为9~11台,将其依次代入模型中进行求解,得到的结果见表3、表4。当电解槽配置台数为9台时,利用电解槽过载特性可以满足HCNG系统掺氢需求,但由于电解槽效率特性,其运行效率随着输入功率的增大会缓慢降低,使得过载部分的功率制氢能力减小,相比于配置10台、11台电解槽时的售氢收入分别减少了417.94万元、635.98万元。但配置9台电解槽的投资维护成本分别比配置10台、11台时减少了532.37万元、941.76万元。综上所述,方案3配置9台电解槽时系统收益最大、经济性最优,此时系统掺氢比为3.27%。
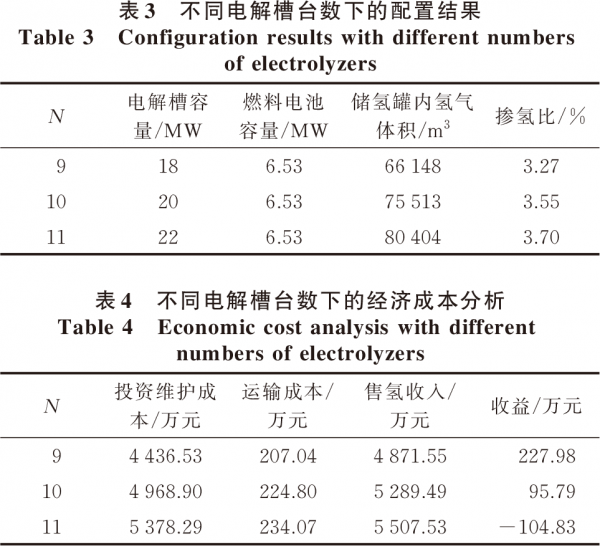
2)多电解槽组合运行分析
为说明多电解槽组合运行策略对系统的影响,进一步探究不同季节下电解槽负载率的大小。由于秋、冬季场景电解槽运行状况大致相同,本文选取春、夏、冬季3个季节进行分析。
春季:在春季典型日,电解槽阵列输入功率较大。由图2可知,采取方案2时,1~8号电解槽一直处于额定运行状态,9、10号电解槽运行功率稍有波动,而11号电解槽一直处于波动运行状态,电解槽阵列处于波动状态时长的标准差为6.27,电解槽长期运行在波动功率下也会影响电解槽的寿命[23]。而采取方案3时,每台电解槽处于波动及过载的时长较为平均,标准差仅为0.68。
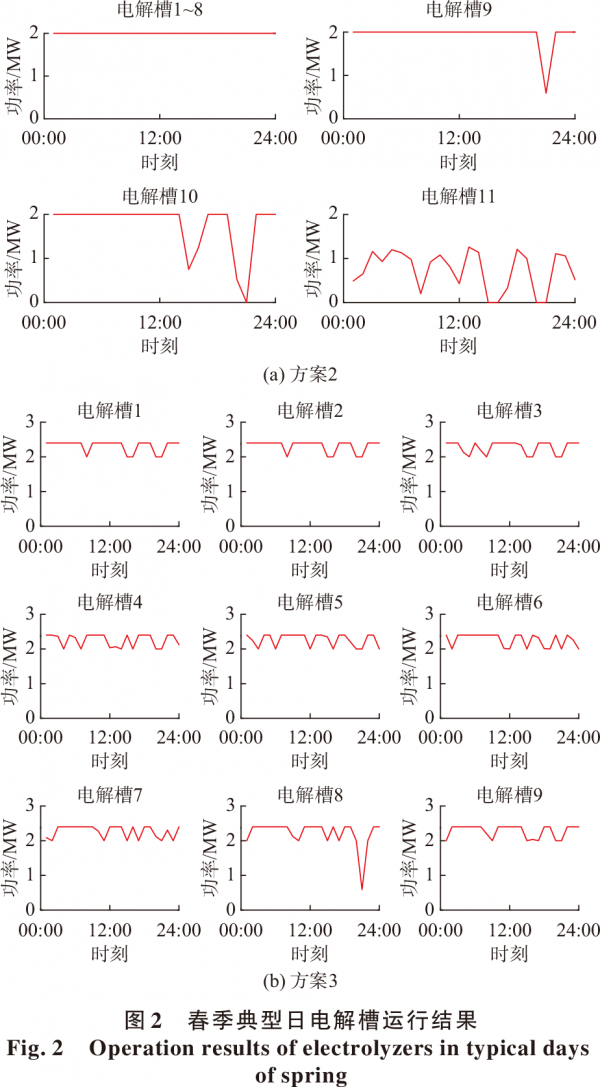
夏季:在夏季典型日,风电出力较小,电解槽阵列输入功率减小。由图3可知,采取方案2时,由于弃风量减小,9~11号电解槽一直处于停机状态,00:00—24:00内8号电解槽仅工作2h。而采取方案3时,每台电解槽的工作时长较为平均,不会出现因弃风量小导致某台电解槽一直处于停机的现象。此外,采用双层轮值策略在保证系统安全运行的前提下还能够减小弃风量。在23:00,额定运行功率分配完成后,在传统的启停策略下,剩余0.06MW的功率不足以重新启动一台电解槽,这部分功率将被弃掉,电解槽阵列由4台电解槽以额定功率运行;而在基于电解槽过载特性的双层轮值策略下,0.06MW的功率被分配到处于额定功率运行的电解槽中,其中,4号电解槽以2.06MW的功率过载运行,5~7号电解槽以额定功率运行。
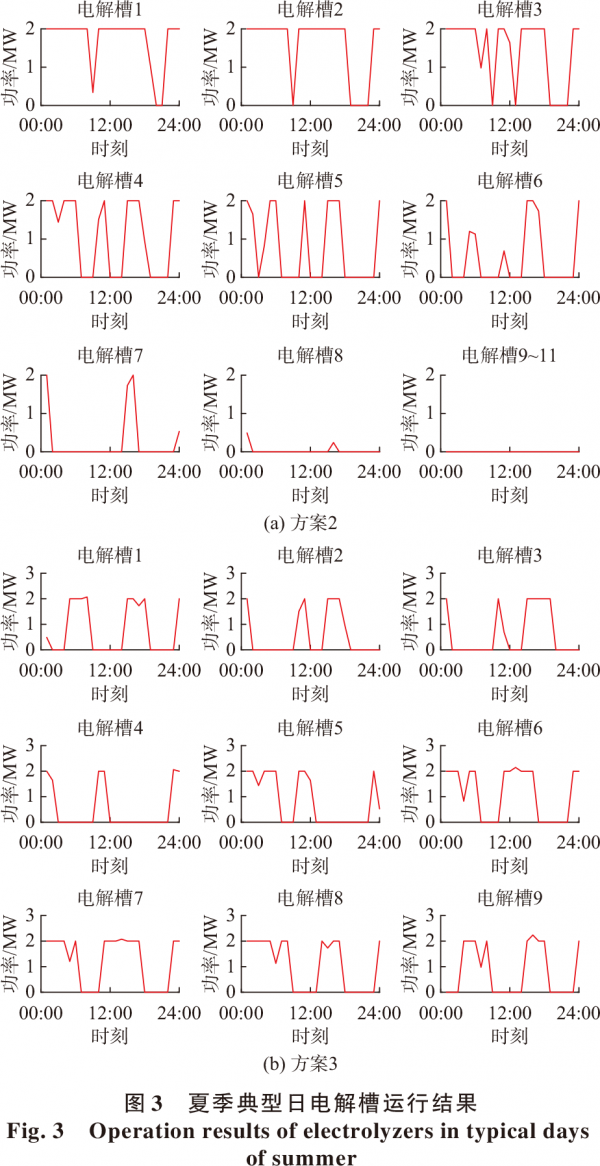
冬季:在冬季典型日,风电出力增大,而天然气负荷也增大。由图4可知,采取方案2时,11号电解槽工作时长最短,在20:00—21:00,所有电解槽都停机后,22:00又从1号电解槽开始启动,故编号越靠后电解槽利用率越低,导致电解槽阵列寿命缩短。采取方案3时,在20:00—21:00所有电解槽都停机后,22:00从7号电解槽开始启动。这是因为在19:00,3~6号电解槽启动,故经过外层轮值后,不从1号电解槽启动而是直接启动7号电解槽。在双层轮值策略下,每台电解槽的功率波动趋势更为缓和、运行时长也更平均,且电解槽运行时的功率均大于安全运行功率。
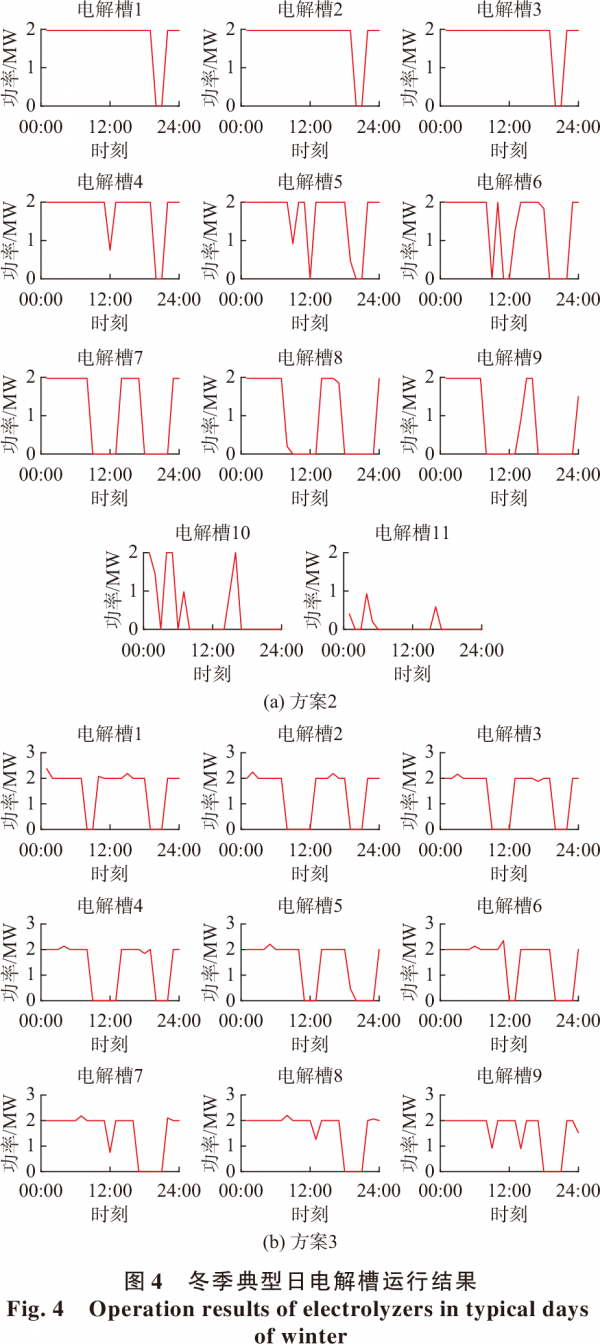
3)运输距离对配置结果影响分析
在实际运行中,输氢距离的远近会影响到输氢成本的大小,不同运输距离下分别采用气瓶车和管道掺氢运输时的系统收益结果也不完全相同。如图5所示,当运输距离为100km时,采用气瓶车运输比管道掺氢运输时的系统收益高出708万元,这是因为采用气瓶车运输时即产即送,无须配置大量储氢罐储氢,容量配置成本更低。然而,随着运输距离的增加,采用气瓶车的单位输氢成本远大于管道运输,当运输距离达到400km时,系统已无法产生收益,出现亏损。相比之下,采用管道掺氢运输时,系统收益随着距离增加而缓慢降低,当运输距离达到500km时才出现亏损。因此,利用天然气管道掺氢在长距离输氢中具有明显优势。
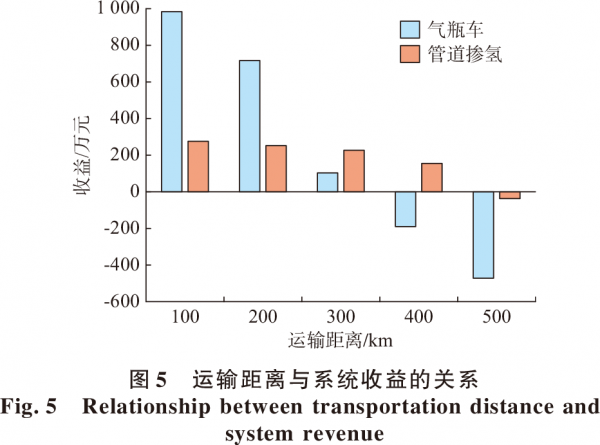
5结语
为提高可再生能源的消纳能力,早日达成“双碳”目标,本文提出将HCNG技术应用于风氢储系统,将氢能与天然气网络耦合,在考虑掺氢比和多电解槽组合运行策略的基础上,提出以系统收益最大为目标的容量配置模型。通过理论和仿真分析,得出具体结论如下:
1)基于电解槽过载特性的多电解槽双层轮值策略,能够均衡电解槽运行时长,避免电解槽处于低功率运行,延长电解槽阵列的寿命。
2)利用电解槽过载特性,能够减小电解槽容量配置。同时,考虑到电解槽效率特性,根据本文所建容量配置模型能够得到使系统经济性最优的配置方案及掺氢比。
3)通过对氢气运输距离的对比分析,证明了利用天然气管道掺氢在长距离输氢中有较优的经济性及可行性。
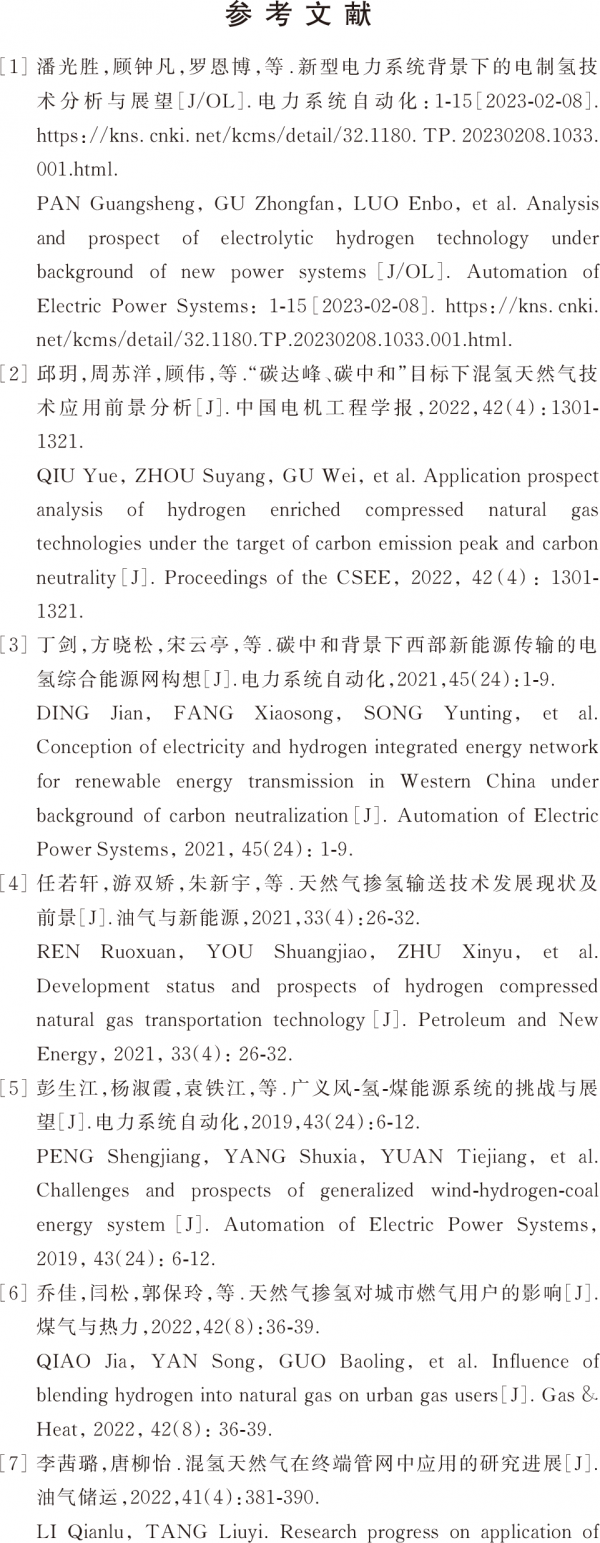
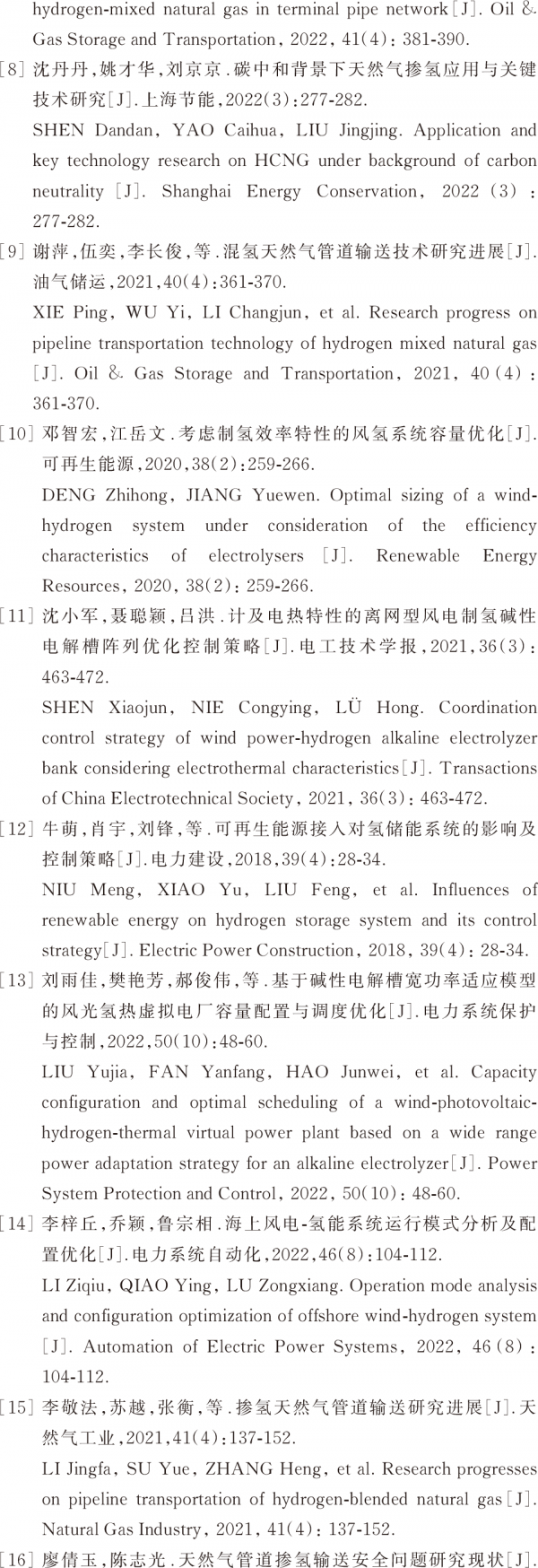
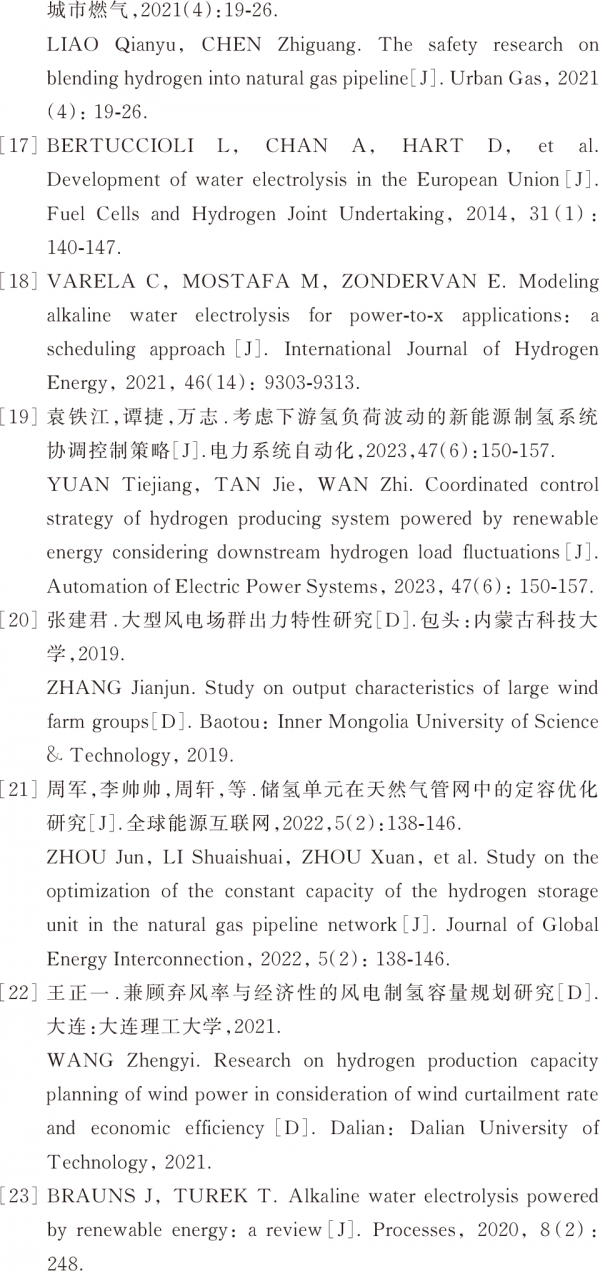
后续研究中可对HCNG网络进行建模,考虑不同管道压强下掺氢比范围不同,进一步完善氢能系统容量配置模型。 |